Destylator przemysłowy to urządzenie, które służy do oddzielania składników mieszanin cieczy na podstawie różnic w ich temperaturach wrzenia. Proces destylacji jest kluczowy w wielu branżach, takich jak przemysł chemiczny, petrochemiczny czy spożywczy. W destylacji wykorzystuje się zjawisko parowania, gdzie ciecz podgrzewana do określonej temperatury przechodzi w stan gazowy, a następnie skrapla się, co pozwala na oddzielenie poszczególnych składników. W przemyśle chemicznym destylatory są wykorzystywane do oczyszczania substancji chemicznych oraz produkcji rozpuszczalników. W branży petrochemicznej proces ten jest niezbędny do uzyskiwania różnych frakcji ropy naftowej, takich jak benzyna, olej napędowy czy nafta. W przemyśle spożywczym destylatory służą do produkcji alkoholu oraz ekstraktów smakowych.
Jakie są rodzaje destylatorów przemysłowych i ich cechy
Wśród różnych typów destylatorów przemysłowych wyróżnia się kilka podstawowych kategorii, które różnią się konstrukcją oraz przeznaczeniem. Destylatory prostokątne to najpopularniejszy typ, który charakteryzuje się prostą budową i łatwością obsługi. Umożliwiają one efektywną separację składników o zbliżonych temperaturach wrzenia. Kolejnym rodzajem są destylatory kolumnowe, które składają się z długiej kolumny wypełnionej materiałem separacyjnym. Dzięki temu proces destylacji jest bardziej efektywny, a uzyskiwane frakcje są czystsze. Istnieją również destylatory próżniowe, które działają w obniżonym ciśnieniu, co pozwala na destylację substancji w niższych temperaturach. To rozwiązanie jest szczególnie przydatne w przypadku substancji termolabilnych, które mogą ulec degradacji w wysokich temperaturach.
Jakie są zalety stosowania destylatorów przemysłowych
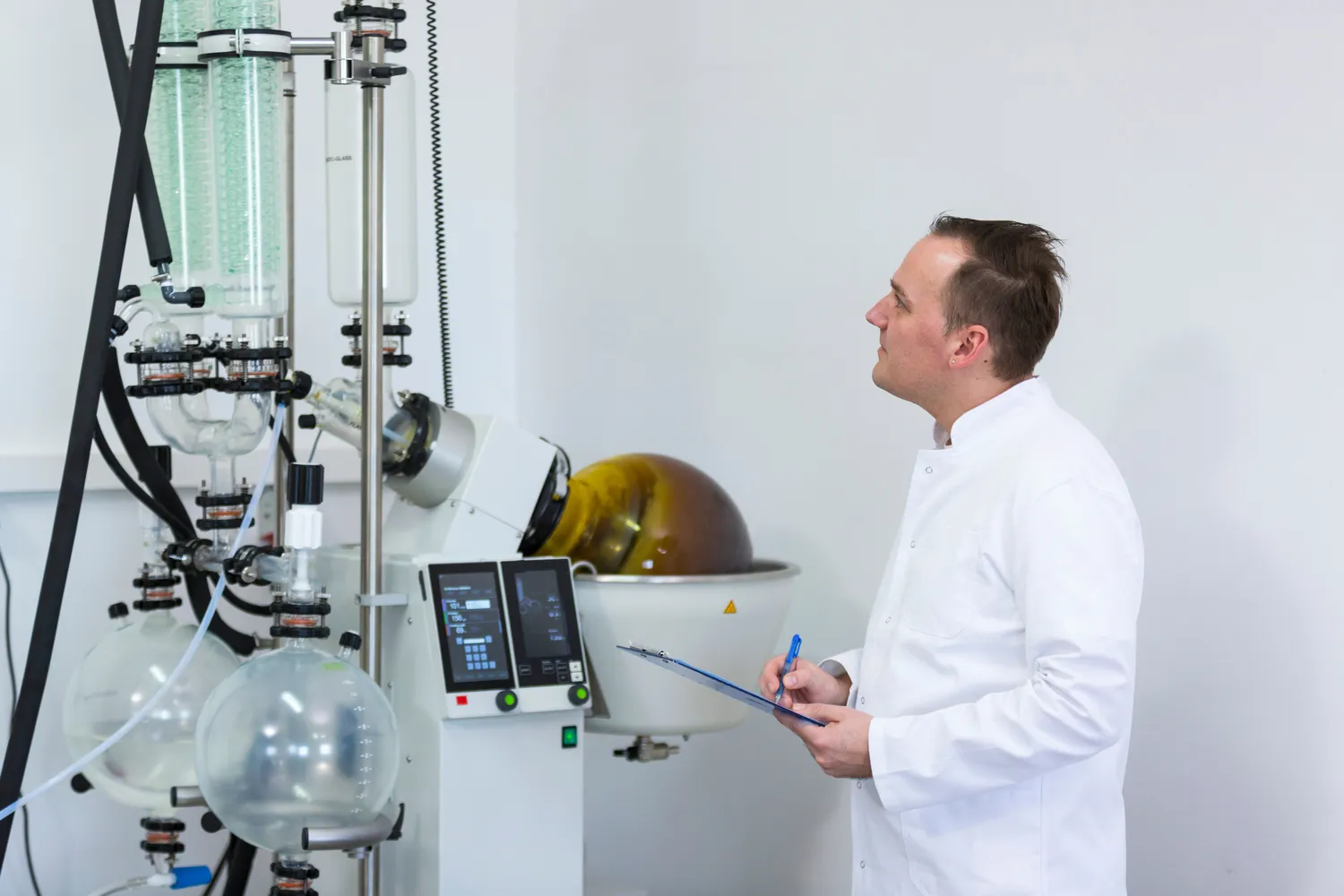
Stosowanie destylatorów przemysłowych niesie ze sobą wiele korzyści dla firm zajmujących się produkcją chemikaliów czy alkoholi. Przede wszystkim pozwalają one na uzyskanie wysokiej czystości produktów końcowych, co jest kluczowe w wielu branżach. Dzięki zastosowaniu nowoczesnych technologii destylacji możliwe jest osiągnięcie efektywności na poziomie 90% lub wyższym, co znacząco wpływa na rentowność procesów produkcyjnych. Kolejną zaletą jest możliwość automatyzacji procesu destylacji, co pozwala na zmniejszenie kosztów pracy oraz zwiększenie bezpieczeństwa operacji. Warto również zwrócić uwagę na elastyczność tych urządzeń – wiele modeli można dostosować do różnych rodzajów surowców oraz wymagań procesowych.
Jakie są koszty związane z zakupem i eksploatacją destylatora przemysłowego
Koszty zakupu i eksploatacji destylatora przemysłowego mogą być znaczne i zależą od wielu czynników, takich jak typ urządzenia, jego wydajność oraz dodatkowe funkcje. Na rynku dostępne są zarówno proste modele o niskiej wydajności, jak i zaawansowane systemy kolumnowe o dużej mocy przerobowej. Koszt zakupu prostego destylatora może wynosić kilka tysięcy złotych, podczas gdy bardziej skomplikowane urządzenia mogą kosztować setki tysięcy złotych lub więcej. Oprócz kosztu samego zakupu należy uwzględnić także wydatki związane z instalacją oraz uruchomieniem urządzenia. Koszty eksploatacyjne obejmują zużycie energii elektrycznej oraz surowców potrzebnych do procesu destylacji. Warto również pamiętać o regularnym serwisowaniu urządzenia oraz ewentualnych naprawach, które mogą generować dodatkowe wydatki.
Jakie są najczęstsze problemy z destylatorami przemysłowymi
Destylatory przemysłowe, mimo swojej efektywności, mogą napotykać różne problemy, które wpływają na jakość procesu destylacji oraz wydajność produkcji. Jednym z najczęstszych problemów jest zatykanie kolumny destylacyjnej, co może prowadzić do obniżenia efektywności separacji składników. Zatykanie może być spowodowane osadzaniem się zanieczyszczeń lub produktów ubocznych, co wymaga regularnego czyszczenia i konserwacji urządzenia. Innym istotnym problemem jest niewłaściwe ustawienie parametrów pracy, takich jak temperatura czy ciśnienie, co może prowadzić do nieefektywnej destylacji i obniżonej jakości produktów końcowych. W przypadku destylatorów próżniowych, utrzymanie odpowiedniego poziomu próżni jest kluczowe dla zachowania właściwości termicznych przetwarzanych substancji. Problemy z uszczelnieniami oraz nieszczelności w systemie mogą prowadzić do strat surowców oraz obniżenia wydajności.
Jakie są innowacje technologiczne w dziedzinie destylacji przemysłowej
W ostatnich latach w dziedzinie destylacji przemysłowej pojawiło się wiele innowacji technologicznych, które znacząco poprawiają efektywność i jakość procesów produkcyjnych. Jednym z najważniejszych trendów jest automatyzacja procesów destylacyjnych, która pozwala na precyzyjne monitorowanie i kontrolowanie parametrów pracy urządzenia. Dzięki zastosowaniu zaawansowanych systemów sterowania możliwe jest optymalizowanie procesów w czasie rzeczywistym, co przekłada się na wyższą jakość produktów oraz mniejsze zużycie energii. Kolejną innowacją są nowoczesne materiały wykorzystywane w budowie kolumn destylacyjnych, które charakteryzują się lepszymi właściwościami termicznymi oraz chemicznymi. Dzięki temu możliwe jest osiąganie wyższej efektywności separacji składników. Warto również zwrócić uwagę na rozwój technologii membranowych, które mogą stanowić alternatywę dla tradycyjnych metod destylacji, oferując możliwość separacji składników w niższych temperaturach oraz przy mniejszym zużyciu energii.
Jakie są wymagania dotyczące bezpieczeństwa w pracy z destylatorami
Bezpieczeństwo w pracy z destylatorami przemysłowymi jest kluczowym aspektem, który należy uwzględnić na każdym etapie eksploatacji tych urządzeń. Pracownicy obsługujący destylatory powinni być odpowiednio przeszkoleni w zakresie procedur bezpieczeństwa oraz znajomości ryzyk związanych z pracą z substancjami chemicznymi i wysokotemperaturowymi procesami. Ważne jest również stosowanie odpowiednich środków ochrony osobistej, takich jak rękawice, gogle czy odzież ochronna, aby zminimalizować ryzyko kontaktu z niebezpiecznymi substancjami. Systemy wentylacyjne powinny być odpowiednio zaprojektowane i utrzymywane w dobrym stanie technicznym, aby zapewnić skuteczną wymianę powietrza i usuwanie oparów chemicznych. Regularne przeglądy techniczne oraz konserwacja urządzeń są niezbędne do zapewnienia ich sprawności i bezpieczeństwa użytkowania.
Jakie są różnice między destylacją a innymi metodami separacji
Destylacja to jedna z wielu metod separacji składników mieszanin cieczy, ale różni się od innych technik pod względem zasad działania oraz zastosowań. W przeciwieństwie do filtracji czy ekstrakcji, które opierają się na różnicach w rozpuszczalności lub wielkości cząsteczek, destylacja wykorzystuje różnice w temperaturach wrzenia składników. Dzięki temu można uzyskać czystsze frakcje substancji chemicznych o podobnych właściwościach fizycznych. Inną popularną metodą separacji jest chromatografia, która polega na rozdzielaniu składników na podstawie ich interakcji z fazą stacjonarną i ruchomą. Chromatografia jest często stosowana do analizy skomplikowanych mieszanin chemicznych oraz oczyszczania substancji o wysokiej czystości. W przypadku ekstrakcji cieczy można oddzielać składniki poprzez ich rozpuszczanie w różnych rozpuszczalnikach, co również ma swoje zastosowania w przemyśle chemicznym i farmaceutycznym.
Jakie są przyszłe kierunki rozwoju technologii destylacyjnej
Przyszłość technologii destylacyjnej wydaje się obiecująca dzięki ciągłemu rozwojowi innowacyjnych rozwiązań oraz rosnącym wymaganiom rynku dotyczących efektywności energetycznej i ochrony środowiska. W miarę jak branża przemysłowa staje przed wyzwaniami związanymi ze zmianami klimatycznymi oraz potrzebą redukcji emisji gazów cieplarnianych, technologie destylacyjne będą musiały dostosować się do nowych norm ekologicznych. Jednym z kierunków rozwoju będzie zwiększenie efektywności energetycznej procesów poprzez zastosowanie odnawialnych źródeł energii oraz recyklingu ciepła odpadowego. Rozwój technologii cyfrowych umożliwi także lepsze monitorowanie i zarządzanie procesami produkcyjnymi dzięki zastosowaniu sztucznej inteligencji oraz analizy danych w czasie rzeczywistym. Ponadto badania nad nowymi materiałami separacyjnymi mogą prowadzić do opracowania bardziej wydajnych systemów destylacyjnych zdolnych do pracy przy niższych temperaturach czy ciśnieniach.
Jakie są kluczowe czynniki wpływające na efektywność destylacji
Efektywność procesu destylacji jest determinowana przez szereg kluczowych czynników, które mogą znacząco wpłynąć na jakość i ilość uzyskiwanych produktów. Jednym z najważniejszych elementów jest temperatura, która musi być precyzyjnie kontrolowana, aby zapewnić optymalne warunki do separacji składników. Zbyt wysoka temperatura może prowadzić do niepożądanych reakcji chemicznych, natomiast zbyt niska może skutkować nieefektywną destylacją. Kolejnym istotnym czynnikiem jest ciśnienie, które wpływa na temperatury wrzenia substancji. W przypadku destylacji próżniowej obniżenie ciśnienia pozwala na destylację w niższych temperaturach, co jest korzystne dla substancji wrażliwych na ciepło. Wydajność kolumny destylacyjnej również ma kluczowe znaczenie – im więcej etapów separacyjnych, tym lepsza jakość uzyskiwanych frakcji. Oprócz tego, jakość surowców oraz ich skład chemiczny mają ogromny wpływ na efektywność procesu.